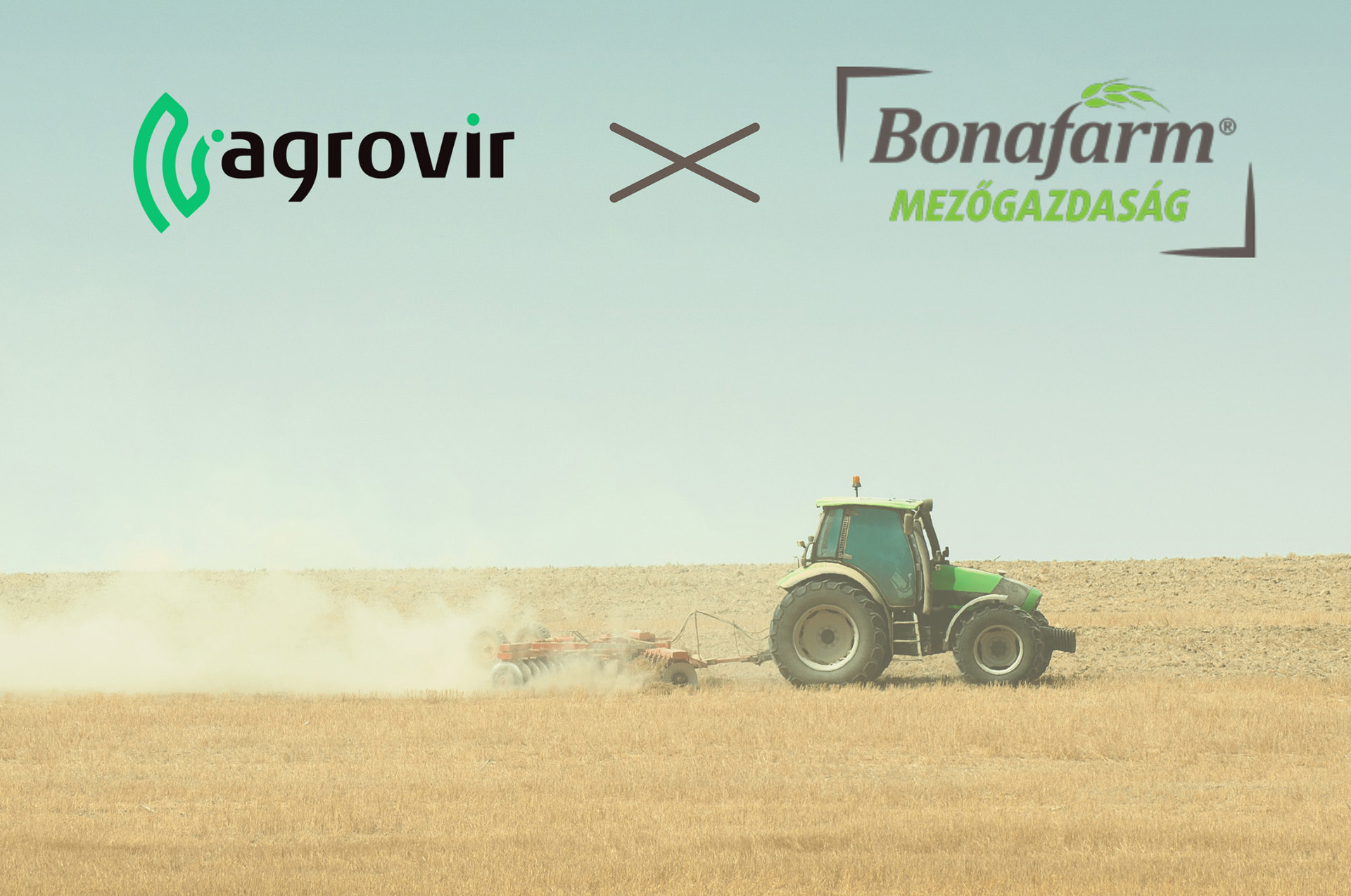
read time 3 minutes
July 25, 2024
Largest AgroVIR implementation project completed at Bonafarm Group
Last week, the AgroVIR system was officially handed over to the Bonafarm Group, marking the completion of one of the company's longest-running projects. This implementation project, initiated in 2021, lasted 3.5 years. Several unique features were integrated into the system to ensure it meets all the specific needs of the group, creating a seamless implementation that complements their existing high-quality and precise IT management.
The Bonafarm Group is one of Hungary's leading group of agri-food companies. Managing multiple different companies belonging to the group is a major task. These companies are engaged in different activities and have different ways of workflow and data management. Standardizing and managing these processes and the incoming data represents one of the biggest challenges for companies of this size. The Bonafarm Group is at the forefront of using digital tools and solutions for production and back-office processes. They have decided to implement AgroVIR to improve and complement the modern technologies they already have.
During the implementation period, several requests were made for specific features, as the group has unique data management processes. For the first time in Hungary AgroVIR made it possible connect directly to the existing SAP system. This project is unique because the real-time and bidirectional data sharing between the two systems has not been implemented in the country yet. The SAP system provides the master data underlying the AgroVIR system, while the stock movements and work performance recorded in the AgroVIR system are immediately reflected in the SAP system, thus reducing the administration time by half. Before implementing AgroVIR , it took several weeks to analyze and evaluate the data. The implementation of AgroVIR allows daily control of production efficiency thanks to the direct and mutual data sharing between the two systems.
The fleet tracking system is also connected directly to AgroVIR. This feature allows you to see real-time, individual data of all the company's machines, such as fuel consumption, engine hours, etc. Enabling multiple systems to share data significantly reduces the administrative burden for such a large group of companies.
The group also utilized the Benchmark service, enabling them to compare their performance with other similar sized competitors and farming companies using AgroVIR . This product allows the group to monitor their work processes' cost levels, input material prices, and performance against competitors. This information highlights the group's strengths and areas for improvement, helping production optimization.
The successful cooperation between AgroVIR and the Bonafarm Group could serve as an example for other agribusinesses. The process of implementation and the preparation of custom specifications took years, but it was an essential step for the further development of the group and its competitiveness.